Stamping parts rely on presses and molds to apply external forces to plates, strips, pipes and profiles to produce plastic deformation or separation, so as to obtain the required shape and size of the workpiece (stamping parts) forming processing method. Stamping and forging are both plastic processing (or pressure processing), collectively known as forging.
Of the world's steel, 60 to 70% is sheet metal, most of which is stamped into finished products. Automobile body, chassis, fuel tank, radiator, boiler drum, container shell, motor, electrical core silicon steel sheet, etc., are stamped processing. Instruments, household appliances, bicycles, office machinery, utensils and other products, there are also a large number of stamping parts.
Compared with castings and forgings, stamping parts have the characteristics of thin, uniform, light and strong. Stamping can produce workpieces with stiffeners, ribs, undulation or flanging that are difficult to manufacture by other methods to improve their rigidity. Due to the use of precision mold, the workpiece accuracy can reach micron level, and the repetition accuracy is high, the specification is consistent, and the hole can be stamped out, the boss and so on.
Cold stamping parts are generally no longer cut, or only a small amount of cutting is required. The accuracy and surface state of hot stamping parts are lower than that of cold stamping parts, but they are still better than castings and forgings, and the cutting amount is less.
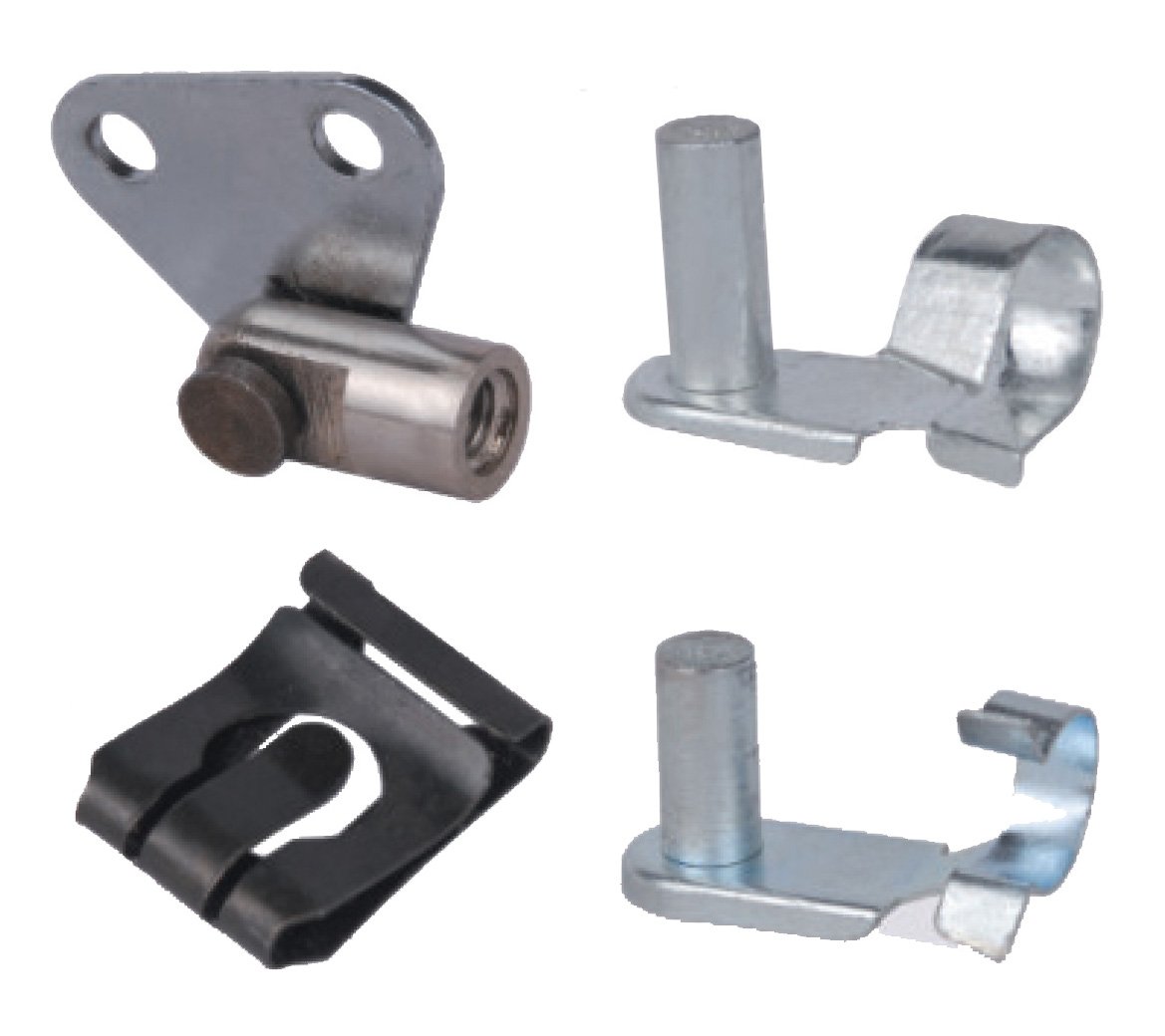
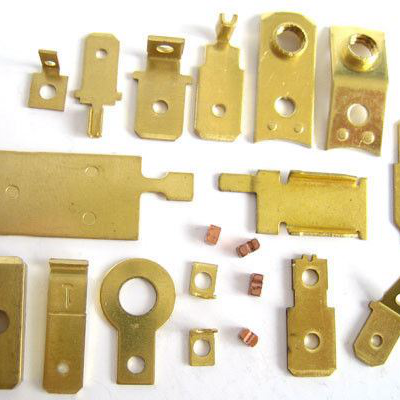
Stamping is an efficient production method, the use of composite die, especially multi-station progressive die, can complete multiple stamping processes on a press, to achieve automatic production from unwinding, leveling, blanking to forming and finishing. High production efficiency, good working conditions, low production costs, generally can produce hundreds of pieces per minute.
Stamping is mainly classified according to the process, which can be divided into two categories: separation process and forming process. The separation process is also called blanking, which aims to separate the stamping parts from the sheet material along a certain contour line, while ensuring the quality requirements of the separation section. The surface and internal properties of sheet metal for stamping have a great influence on the quality of stamping products, which requires accurate and uniform thickness of stamping materials. Smooth surface, no spot, no scar, no abrasion, no surface crack, etc. The yield strength is uniform and has no obvious directivity. High uniform elongation; Low yield ratio; Low work hardening.
Post time: Sep-05-2023